Заводы не выдают идеальные детали «по умолчанию» — тут всё зависит от контроля качества. Именно специалисты по контролю первым встречают брак, замечают скрытые дефекты и не пускают наружу детали, которые могут подвести клиента. Ошибся один — пострадает вся партия, а иногда и репутация компании.
Работа с металлом не прощает спешки. Здесь важно знать: какие требования предъявляются именно к этой детали, где слабые места у технологии, что прописано в ГОСТах и ТУ. Некоторые сотрудники думают, что всё решает опыт, но даже самый опытный инспектор без бумажки — просто «кто-то со стажем». Нужно не только помнить стандарты, но и уметь их быстро найти и применить в спорной ситуации.
Важно уметь договариваться с технологами, рабочими, инженерами. Контролёр — не «надсмотрщик», а человек, который делает производство надёжнее. Без доверия и взаимного понимания ничего хорошего не выйдет. Честно сказать «ребята, пропустили мелкий дефект» — куда эффективней, чем закрыть глаза и надеяться, что «пронесёт».
- Роль специалиста контроля качества на производстве
- Базовые знания и ключевые стандарты
- Типовые инструменты и методы контроля
- Ошибки, которые могут дорого стоить
- Реальные лайфхаки для повседневной работы
Роль специалиста контроля качества на производстве
Сегодня ни одно производство в машиностроении не обходится без человека, который отвечает за контроль качества. Специалист этого профиля — не просто проверяющий чек-листы. Он реально влияет на то, насколько техника из цеха безопасна, долговечна и соответствует нормам. Его задача — выявить слабые места до того, как они станут чьей-то проблемой на объекте или у клиента.
Роль контролера часто недооценивают, но без него больше половины дефектов уходят дальше по цепочке. Если взглянуть на статистику, около 60% всех выявленных браков в машиностроении находят именно сотрудники службы контроля на этапе промежуточной проверки. А если эти дефекты пропустить — стоимость переделки деталей может вырасти почти в 5-10 раз, чем если бы ошибку исправили сразу после операции.
Этап контроля | % выявления брака |
---|---|
Входной контроль сырья | 23% |
Промежуточный контроль (в цеху) | 61% |
Финальный контроль готовых изделий | 16% |
Контролёр должен уметь:
- Замечать брак там, где его не увидит автомат.
- Отличать критические дефекты от несущественных — чтобы не тормозить производство зря.
- Оперативно общаться с другими специалистами по техпроцессу, узнавать причины отклонений.
- Документировать найденные проблемы по форме — иначе будет путаница, и «крайний» всегда найдётся случайно.
Чем грамотнее работает специалист, тем реже случаются аварии и дорогостоящие рекламации. На практике это буквально человек, который экономит предприятию миллионы и бережет нервы коллегам по всему цеху.
Базовые знания и ключевые стандарты
Без прочной базы ничего не получится — любой специалист контроля качества должен понимать, что в машиностроении царят строгие правила. Главное — четко знать, зачем всё это делается: от деталей станка зависит и точность, и безопасность, и долговечность всей конструкции. Тут не прокатит «на глазок».
Контроль качества всегда опирается на документы. В России и странах СНГ базовыми считаются ГОСТы и Технические условия (ТУ). ГОСТ — это государственный стандарт, по сути, инструкция, как делать всё правильно. Например, ГОСТ 26645-85 объясняет требования к размерам и допускам деталей, а ГОСТ 24642-81 детально описывает правила визуального и инструментального контроля сварных швов.
Нельзя забывать и про международные стандарты. Часто встречаются ISO 9001 (система менеджмента качества) и ISO 19443 (качество в атомной отрасли), а если работаешь на экспорт — могут потребовать соответствие DIN (Германия), JIS (Япония) или ASTM (США).
Что обязан знать любой контролёр, чтобы не потерять лицо перед проверяющими:
- Основы метрологии: как работает штангенциркуль, микрометр, калибры и другие измерительные инструменты;
- Допуски и посадки. Тут пригодится ГОСТ 25347-82 — таблица допусков и их условные обозначения;
- Правила маркировки материалов. ГОСТ 7566-2019 — что требуется указывать на готовых изделиях;
- Требования к визуальному и неразрушающему контролю;
- Документация: как оформлять акт, протокол или наряд на доработку.
Чтобы не запутаться в цифрах и параметрах, вот небольшая памятка по основным стандартам для машиностроения:
Стандарт | Область применения |
---|---|
ГОСТ 26645-85 | Размеры и допуски деталей |
ГОСТ 24642-81 | Контроль сварных швов |
ISO 9001 | Система менеджмента качества |
ГОСТ 25347-82 | Таблицы допусков |
ГОСТ 7566-2019 | Правила маркировки |
Часто новичкам кажется, что все эти ГОСТы нужны только для отчёта. На практике это система страховок: если что-то не так — есть бумага, где всё расписано по шагам. Так что проще с самого начала привыкнуть сверяться с требованиями и держать под рукой список нужных стандартов. Это помогает не только в работе, но и когда приходится спорить с технологами или заказчиками.
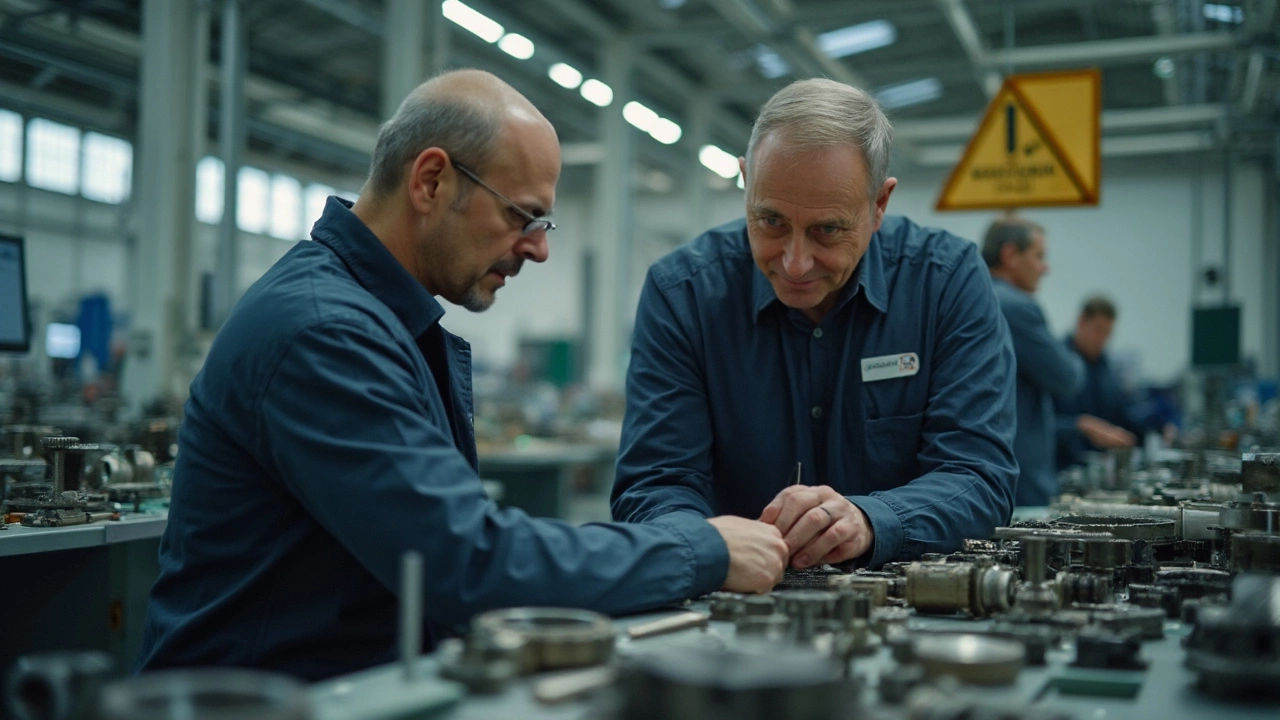
Типовые инструменты и методы контроля
Контроль качества невозможен без надёжных инструментов. Механический цех — не место для догадок. На первом месте всегда простой штангенциркуль. Он проверяет длину, диаметр, ширину и глубину. Следом идут микрометры — с их помощью можно «поймать» точность до сотых миллиметра. Для массовых деталей обычно есть калибры: прошли — идут дальше, не прошли — на доработку или в брак.
- Штангенциркуль: измеряет базовые параметры практически любых деталей.
- Микрометр: позволяет измерять с высокой точностью, до 0,01 мм.
- Калибры: обеспечивают быстрый контроль соответствия размерам.
- Индикаторы часового типа: легко увидеть кривизну, биение, отклонения в одну-две сотки.
- Толщиномеры: нужны для проверки лакокрасочных покрытий и специальных слоёв.
Обычный контроль геометрии на этом не заканчивается. Сегодня в цехах всё чаще появляются 3D-сканеры и оптические измерительные системы. Они в разы ускоряют контроль качества крупных или сложных деталей. Например, с помощью ручного лазерного 3D-сканера можно снять до 500 000 точек в секунду и сразу сравнить модель с эталоном в цифровом виде.
Не обходится и без неразрушающего контроля. Тут работают дефектоскопы, ультразвуковые и магнитные приборы — они ищут микротрещины и пустоты внутри металла без единого разреза. На заводах любят ультразвук — одна проверка занимает не больше 10 секунд.
Для удобства сравнения, вот основные методы и их особенности:
Метод контроля | Что даёт | Время проверки |
---|---|---|
Механические измерения | Размеры, посадки, биения | 1-5 мин |
3D-сканирование | Точные модели, сравнение с чертежом | до 3 мин |
Ультразвуковой контроль | Внутренние дефекты | 10-30 сек |
Магнитный контроль | Трещины на поверхности | 2-10 мин |
Под рукой всегда должны быть лупа, фонарик, маркеры для пометок и обычная чистая ветошь — чтобы сразу убрать грязь и видеть поверхность. Рабочее место хорошего контролёра всегда чистое, инструменты целые и поверены, иначе от них мало толку.
Ошибки, которые могут дорого стоить
Одна из главных проблем — пропустить явный дефект или, наоборот, придраться к мелочи, не значимой для работы изделия. В отчётах заводов по контролю качества встречаются такие моменты регулярно. Самый неприятный сценарий — когда брак попадает к клиенту. По данным машиностроительных предприятий в России, из-за этого до 30% рекламаций связаны именно с человеческим фактором на этапе контроля.
Типичные ошибки контролёра можно перечислить на пальцах, но каждая из них критична:
- Не сверился с чертежом или техническими требованиями — ошибся при оценке детали.
- Поторопился и пропустил дефекты, которые видно даже невооружённым глазом.
- Использовал неповеренный инструмент — измерения оказались неверными.
- Проигнорировал необычные отклонения, подумав «и так сойдёт».
- Недостаточно зафиксировал замечания — потом не смог доказать свою правоту.
Таблица ниже показывает, как часто встречаются эти ошибки на практике и во что они обходятся:
Ошибка | Частота на 100 проверок | Ориентировочные потери (руб.) |
---|---|---|
Пропущенный дефект (визуально) | 15 | от 50 000 до 300 000 |
Измерения неповеренным инструментом | 8 | 20 000 – 100 000 |
Невнимательность к отклонениям | 12 | 10 000 – 250 000 |
Неправильное оформление документации | 6 | 5 000 – 70 000 |
Часто от таких просчётов страдает не только производитель, но и конечные заказчики — простой техники, ремонт, возвраты. Иногда дело доходит до отзывов целых партий, а это всегда репутационные удары и миллионные убытки.
Чтобы сэкономить нервы себе и компании, нужно:
- Всегда сверять детали с документацией, даже если думаешь, что знаешь всё наизусть.
- Следить за состоянием инструментов и вовремя отдавать их на поверку.
- Не игнорировать даже мелкие отклонения, лучше разобраться на месте.
- Фиксировать всё подозрительное в отчётах и обсуждать это с коллегами.
Ошибки в контроле обходятся слишком дорого, чтобы относиться к работе формально. Тут без внимания и аккуратности — никак.
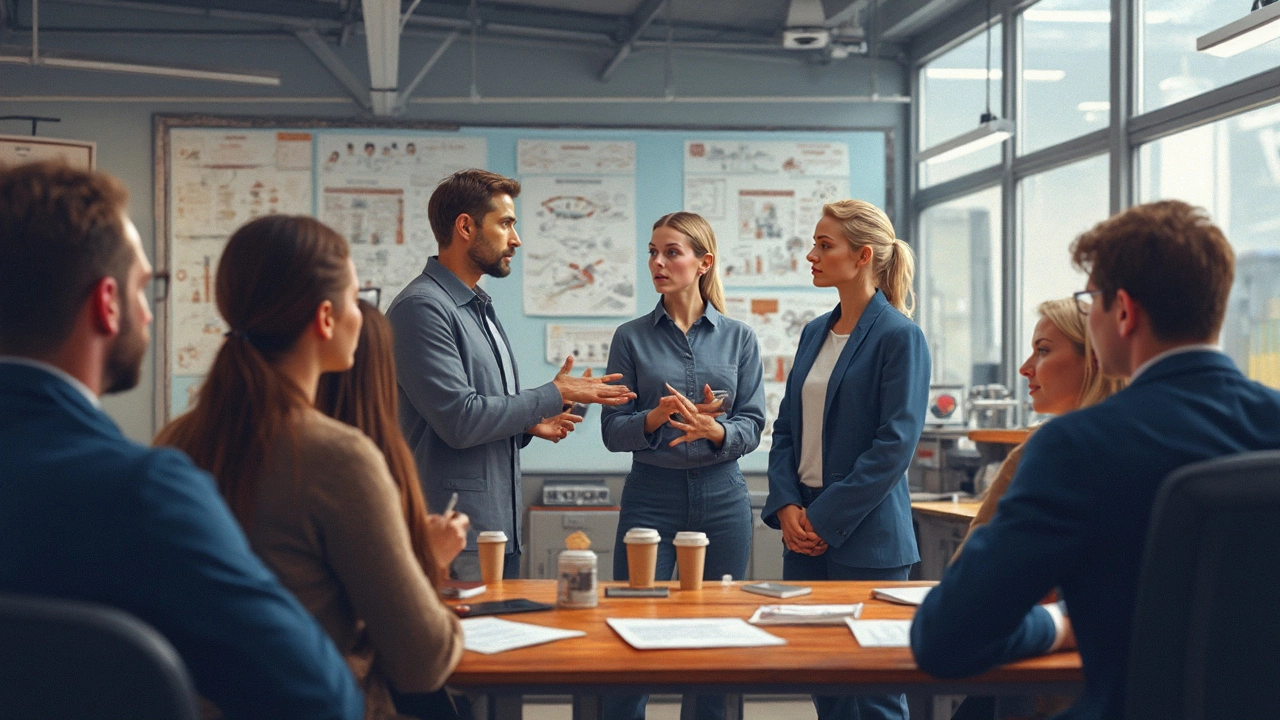
Реальные лайфхаки для повседневной работы
Здесь не обойтись без простых, но реально рабочих советов, которые выручали не раз. Нет смысла делать всё вслепую — опытные контролёры давно используют маленькие хитрости, чтобы быстрее и точнее выполнять свою работу.
- Не полагайтесь только на память. Храните ключевые выдержки из ГОСТов, ТУ и инструкции по проверке рядом: бумажная папка или быстрый доступ к файлу на рабочем компьютере — экономит нервы и время.
- Проверяйте калибровку своих инструментов каждое утро. Даже микрометр после пары падений может сильно наврать. Не стесняйтесь время от времени замерять "эталонную" деталь, чтобы убедиться, что всё в порядке.
- Фото и видео фиксация позволяет наглядно показать коллегам спорные моменты. Не забывайте: лучше один раз показать, чем долго объяснять на словах.
- Организуйте своё рабочее место так, чтобы часто используемые инструменты всегда были под рукой. Порядок на столе сэкономит вам до 20 минут за смену, особенно если смены бывают авральными.
- Не замалчивайте свою ошибку — все рано или поздно ошибаются. Главное — быстро заметить промах и не дать ему стать систематическим.
А теперь пара цифр. По данным внутреннего аудита в крупной компании из списка ТОП-10 машиностроителей России, почти 27% брака удавалось предотвратить именно благодаря небольшим, но регулярным процедурам проверки калибровки инструмента и использованию чек-листов. Вот пример, как всё выглядит в цифрах:
Лайфхак | % предотвращённого брака за год |
---|---|
Проверка инструментов каждое утро | 13% |
Фотофиксация дефектов | 7% |
Использование чек-листов | 7% |
Соблюдая простые правила и не стесняясь учиться новому, можно стать для цеха не просто человеком на должности, а настоящим контроль качества в действии: тем, кто реально держит руку на пульсе.
Написать комментарий