Интересный парадокс: сварочная точка на кузове автомобиля определяется с точностью до миллиметра, а то и точнее. Ошибся — на конвейере соберётся брак. Кажется, что в машиностроении всё решает металл и инженерная мысль, но если нет системы выверенного контроля, завод рискует вместо прибыли огрести волну рекламаций. Почему некоторые фирмы десятилетиями удерживают славу надёжных, а другие быстро теряют уважение рынка? Всё дело в менеджменте качества — его роль в современных заводах нельзя переоценить ни при каких обстоятельствах.
Что такое менеджмент качества и зачем он нужен в машиностроении
Термин "менеджмент качества" кажется канцелярским, но за ним стоит простая штука: это система мер, гарантирующих, что каждый болт, каждая шестерня — ровно такого качества, какого ждёт покупатель, без сюрпризов и халтуры. Особая жёсткость тут не случайна — изделия машиностроения слишком часто идут в ответственные сферы: транспорт, производство, строительство. Представьте завод, где тысяча деталей не проходит контроль — и каждая может стать причиной масштабных поломок. Тут главная фишка — предупредить, а не устранять уже случившееся.
Требования к качеству в машиностроении — одни из самых строгих. Для справки: по российскому ГОСТ Р ИСО 9001 стандарты для заводов фактически скопированы с международного ISO 9001, а в Европе к ним добавляются ещё и внутренние нормирования концернов. Системы контроля построены на последовательном отсеве: начиная с закупочных материалов (металл проверяют на сертификат партии и даже брешь на микроуровне), над контуром производства стоят автоматические и ручные проверки, у инженеров — постоянные замеры результативности каждой партии. Всё ради того, чтобы не нарваться на фатальный сбой.
Менеджмент качества проникает во всю работу завода — от бумажек на входе до упаковки. Здесь нет случайных решений: даже простую отвертку выбирают по строгим критериям, чтобы не сломалась в момент сборки. Кстати, многие производственные катастрофы (особенно в советское время) происходили именно из-за игнорирования систем контроля. Хорошо отлаженный процесс кажется рутиной, но на самом деле он спасает тысячи жизней и миллионов рублей — проверено историей «АвтоВАЗа», КАМАЗа, даже Tesla. Сейчас на многих крупных европейских заводах доля брака — менее 1% от общего объема. Это высочайший уровень, и такая стабильность достигается только через чётко выстроенный менеджмент качества.
Основные элементы и структура менеджмента качества на заводе
Система менеджмента качества — не хаотичная проверка каждого винта. Это полноценная, разветвлённая архитектура, объединяющая десятки методик. В ядре — шестиступенчатый цикл Деминга (PDCA): планируй, делай, проверяй, корректируй, внедряй и снова крутись по кругу. Такой цикл внедряют практически на каждом этапе — от проектирования до упаковки готовой детали на складе.
Ключевые элементы системы качества таковы:
- Система стандартизации: все рабочие процессы и детали описаны до последнего болтика.
- Контроль входящего сырья: сталь или пластик проходят лабораторные анализы перед запуском в цеха.
- Инструкции для каждого этапа производства — буквально схемы действий на линии.
- Промежуточные проверки: например, после сварки кузова обязательна рентгенограмма сварного шва.
- Финальный контроль — слесари, мастера и автоматические станции одновременно оценивают соответствие продукции.
- Обратная связь от клиентов: рекламации, сервисные запросы мгновенно попадают в систему анализа.
Один из ярких случаев мне недавно рассказал знакомый инженер с автосборочного завода в Тольятти. Проверку одного винта усилителя руля устроили даже через 8 лет после начала эксплуатации партии автомобилей, потому что отдельные владельцы заметили «люфт». Найти даже небольшой сбой в основании конструкции через годы — заслуга как раз скрупулёзной системы контроля и грамотного анализа рекламаций. Кстати, в машиностроении ценится не только исправление последствий, но и «прокачка» методов — если найден брак, систему быстро обновляют под новые риски.
Вся работа завода записывается не в толстых бумажных журналах, как лет двадцать назад, а в цифровых трекерах. Данные тут на вес золота: кто и когда накосячил, можно отследить вплоть до смены и времени суток. Статистика брака по участкам часто вывешивается прямо в цеху — соревновательный дух среди бригад поднимает точность. А ведь ещё десять лет назад мастер мог заметить проблему только по внешнему виду детали, а не с помощью рентгена или автоматизированного измерителя.
Вот реальный пример из индустрии:
Год | Процент брака на крупных заводах РФ | Процент брака на BMW (Германия) |
---|---|---|
2010 | 3,2% | 1,7% |
2020 | 1,9% | 0,8% |
2025 | 1,3% | 0,5% |
Падение процентов — заслуга не только новых технологий, но и системного подхода к менеджменту качества. Каждый лишний процент брака — это не только деньги, но репутация компании. Отсюда — культ точности и прозрачности на заводах: менеджмент качества становится центром производственной культуры.
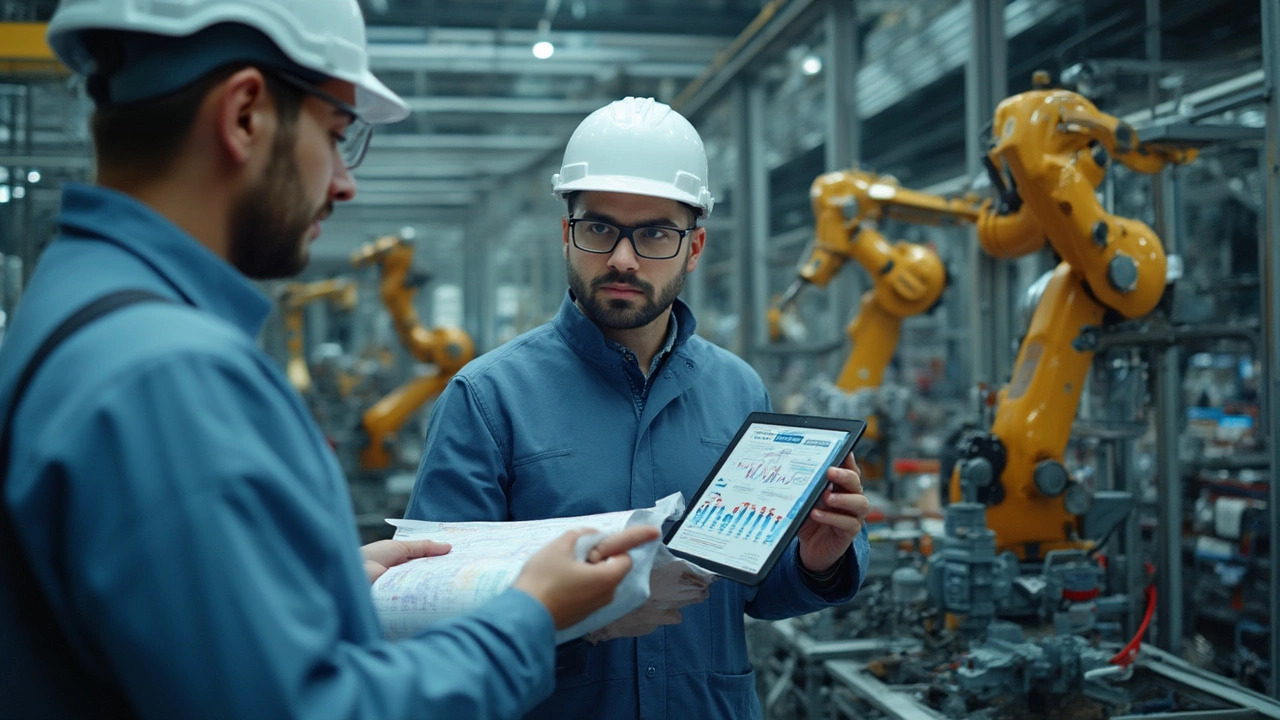
Стандарты ISO и отечественные нормы: почему без них никуда
Без стандартов в машиностроении просто не выжить — слишком сложное и затратное производство, чтобы идти на авось. Самые известные стандарты — ISO 9001 и ISO/TS 16949 (для автопрома). ISO 9001 регулирует структуру менеджмента качества, распределение ответственности на заводе, сроки и методы контроля. В России действует ГОСТ Р ИСО 9001-2015 — по сути это тот же стандарт, только адаптированный под российские реалии.
Вот несколько реально обязательных пунктов стандарта:
- Все производственные процессы должны быть документированы по шагам.
- Каждый сотрудник обязан проходить обучение контролю на своем рабочем месте — без бумажки на линию не выпустят.
- Планирование качества — не абстракция: для каждого этапа прописан строгий регламент, частота проверок и инструменты измерения.
- Учет отклонений с созданием карты несоответствия: чтобы найти причину брака, а не просто выкинуть партию.
В автомобильной промышленности к этим пунктам добавляется IATF 16949 — это супержёсткая версия ISO, внедрённая немецкими, французскими и американскими автомобилестроителями. До смешного доходит: в цех могут пустить только после прохождения теста по стандарту (обычно 2-3 часа). Если найдут мелкую неисправность в отчёте — сразу штраф или дисциплинарные меры, вплоть до отзывов продукции. Только так европейцы и японцы держат качество буквально на уровне микрона.
Кстати, несколько лет назад завод Volvo в Калужской области подвёл итоги внутреннего аудита — больше 90% сотрудников считают стандартизацию и проверки главным фактором успеха марки. Это не реклама: если бы не было привязки к стандартам, сложные современные автомобили никто бы не пустил на дороги. А уже потом, на основе этих систем контроля, строят системы мотивации для рабочих, внедряют LEAN/бережливое производство, кайдзен и другие методы повышения эффективности.
Советы и интересные факты: как реально повысить качество на заводе
Во время встреч с инженерами крупных машиностроительных предприятий всегда возникает один и тот же вопрос: что именно помогает удерживать качество на высоте, даже когда оборудование устаревает, а сырьё дорожает? Вот несколько рабочих советов, проверенных практикой:
- Не экономьте на обучении — ошибка стажёра может обойтись дороже замены станка. Запуск внутренней программы с практическими тестами обычно снижает количество брака в разы.
- Внедряйте цифровой архив для всех параметров качества — бумажные протоколы легко потерять, а цифровые дают аналитику в один клик.
- Не бойтесь признавать ошибки: реальные кейсы, когда завод открыто признавал брак, хотя покупатель ещё не жаловался, оборачивались ростом доверия со стороны клиентов.
- Используйте автоматизацию в простых операциях — такие решения дают прирост точности от 20 до 40% на каждую смену.
- Регулярный аудит с внешними экспертами: часто опытный консультант находит мелочь, которую «замылился» глаз привычного работника.
Интересный факт: на крупнейшем европейском заводе по выпуску тракторов каждую неделю проводят так называемый «кросс-контроль»: работник с одного участка проверяет работу на другом участке, не зная особенностей. Это помогает выявить «бытовые» косяки, которые сам мастер бы не заметил. Примерно по такой же схеме действуют и в авиастроении — контроль идёт на каждом этапе независимыми группами.
Не менее важно и то, что большинство инноваций рождаются внутри самих производственных команд. Рабочие, которые десятилетиями собирают один и тот же редуктор, знают слабые места лучше, чем любой внешний аудитор. Когда им дают возможность сами предлагать решения для снижения брака — показатели качества улучшаются заметнее, чем от дорогого консалтинга.
А теперь главная идея: менеджмент качества в машиностроении — это не модное зарубежное слово, а жёсткая, продуманная система с тысячами проверенных решений. В современном мире конкуренция идёт не только в цене, но и в надёжности. Завод, который контролирует процесс от закупки сырья до последнего болта в техпаспорте, точно не останется без заказов. Хочешь сделать сильную марку — строй грамотную систему качества.
Написать комментарий