Если еще думаете, что работать по старинке дешевле — попробуйте посчитать, во сколько обходятся простои, лишний брак и возвраты товаров из-за мелких ошибок. В машиностроении мелочей не бывает: из-за устаревших процессов теряется время, портятся детали, у работников падает мотивация.
Инновации — это не про моду, а про выживание. Когда соседний завод делает тот же продукт быстрее и качественнее, становится понятно: пора подтянуть процессы и искать свежие решения. Например, автоматизация простых операций освобождает руки для сложных задач, а внедрение современных систем управления помогает отслеживать все этапы создания детали — от чертежа до упаковки.
- Почему старые методы уже не работают
- Как инновации меняют повседневную работу на заводе
- Экономия и выгода: что дает внедрение новых технологий
- Ошибки и страхи: почему боятся инноваций
- Практические советы по внедрению идей на производстве
Почему старые методы уже не работают
Машиностроение уже давно не тот спокойный рынок, где можно работать по накатанной. Конкуренция жёстче, чем раньше, а клиенты требуют и быстрее, и дешевле. Старые методы часто не успевают за запросами рынка: то, что вчера помогало экономить, сегодня тормозит каждый шаг.
Например, ручная обработка деталей замедляет процесс, а количество брака из-за человеческого фактора всё ещё держится на уровне 2-5%. Неточности при измерениях и устаревшее оборудование приводят к лишним расходам. Статистика проста: в 2024 году исследования в России показали, что предприятия, где почти всё по-старому, теряют до 22% прибыли из-за неэффективных процессов и простоев.
Таблица сравнения расходов компаний с разным уровнем автоматизации:
Уровень автоматизации | Процент брака | Средние простои (часов в месяц) | Потери прибыли |
---|---|---|---|
Минимальный | 5% | 25 | 22% |
Средний | 2.5% | 10 | 11% |
Высокий | 1% | 3 | 4% |
Ещё одна проблема старых методов — постоянная нехватка квалифицированных кадров. Большая часть молодёжи просто не хочет сидеть у станка весь день, а старых работников становится всё меньше. Отсюда проблемы с поиском персонала и постоянные перебои.
И самое главное — пока одни экономят на инновациях, другие уже улучшают процессы и выходят на рынок с выгодными предложениями. В итоге устаревший подход больше всего бьёт по конкурентоспособности бизнеса. Здесь выбор простой: либо в ногу со временем, либо твои заказчики уходят к тем, кто способен меняться.
Как инновации меняют повседневную работу на заводе
Инновации полностью меняют подход к рутине на производстве. Раньше всё крутилось вокруг бумажных отчетов, ручной проверки станков и большой доли человеческого фактора. Сейчас на многих заводах часть этой рутины легко берут на себя автоматизированные системы. Оператор теперь не бегает по цеху с блокнотом – он видит всё на экране и сразу замечает, где что идёт не так.
Взять, например, промышленные роботы. По данным Ассоциации производителей робототехники России, к 2024 году каждый третий крупный машиностроительный завод в стране хотя бы частично перешёл на роботизированную сборку. В результате падает количество ошибок — банально меньше человеческого вмешательства, меньше опечаток в настройках и недосмотров во время сборки.
Инновации также меняют рабочий день инженеров и наладчиков. Теперь испытания новых деталей можно проводить на виртуальных моделях, не тратя металл и не ломая оборудование. Это реально экономит дни, а иногда и недели на каждый новый проект.
Вот как выглядит разница в работе до и после внедрения инноваций:
Процесс | До инноваций | После внедрения |
---|---|---|
Контроль качества | Вручную, выборочно | Автоматизировано, все детали проходят сканирование |
Производительность | Зависит от опыта сотрудников | Стабильно высокая, системы снижают влияние человеческого фактора |
Сроки разработки | От 3–4 недель | Часто 1–2 недели |
Ошибка при сборке | До 5% по статистике крупных заводов | Меньше 1% |
Самое главное — внедрение инноваций позволяет проще учиться новым сотрудникам. Интуитивные интерфейсы оборудования, подсказки на экранах и подробные инструкции прямо на рабочем месте сокращают длительные вводные обучения с месяцев до пары недель.
Промышленные IoT-датчики дают менеджерам полный контроль за тем, что происходит в каждом цехе. Можно быстро видеть, какой станок простаивает, где перегрев, а где детали пошли с браком. Раньше, чтобы выяснить это, требовались долгие разбирательства и бумажные акты.
- Экономится рабочее время.
- Повышается прозрачность всех процессов.
- Меньше аварий и простоев.
- Растёт качество готовой продукции.
Так что если завод пару лет назад работал по принципу «за всё отвечает мастер», то сегодня многое автоматизировано, и люди могут сосредоточиться не на рутине, а на развитии новых идей.
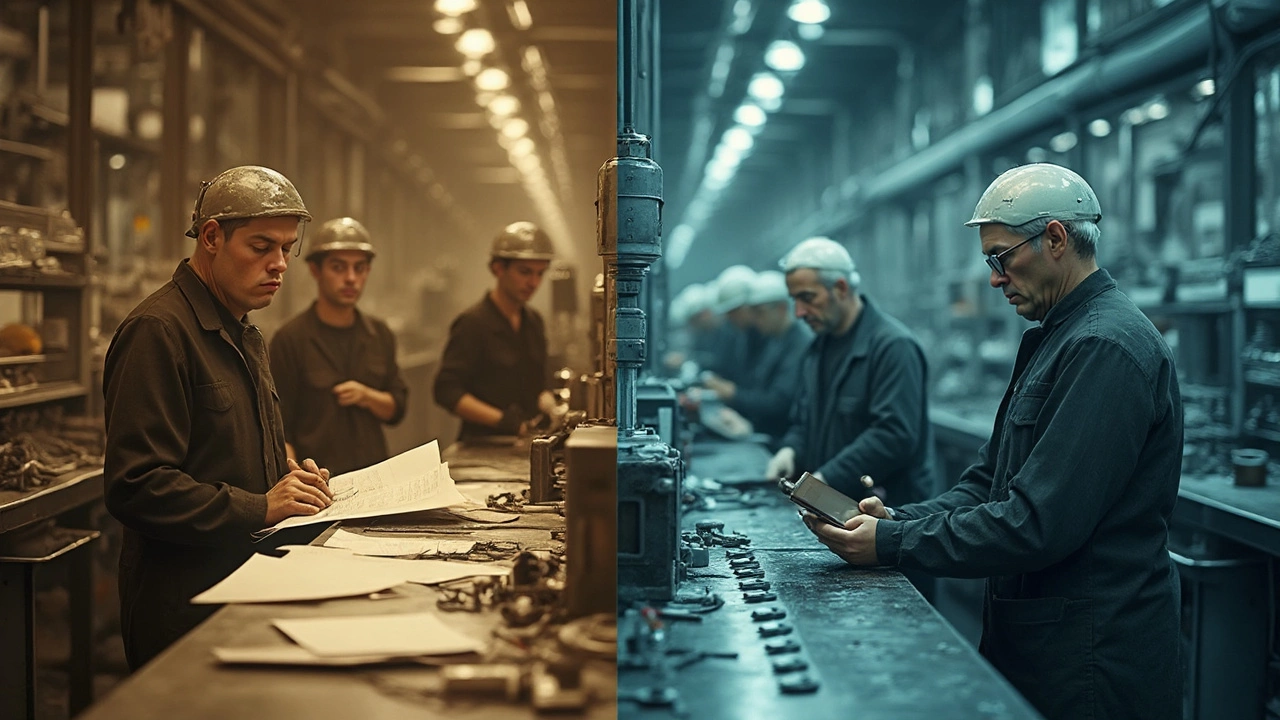
Экономия и выгода: что дает внедрение новых технологий
Основа любого производства — это себестоимость изделия и скорость выпуска. Вот почему инновации в машиностроении перестали быть чем-то экзотическим. Они нужны, чтобы реально экономить деньги и избавляться от неэффективности.
Когда завод внедряет, например, современный станок с ЧПУ, тратится меньше времени на переналадку оборудования. Не нужно десятки часов, чтобы подгонять каждую деталь вручную — настройки цифровые, точность выше. Машина сама подсчитывает и точно повторяет каждое действие.
Экономия проявляется буквально везде:
- Снижаются производственные отходы: точные автоматы меньше ошибаются.
- Сокращаются простои — умные системы заранее предупреждают о поломках.
- Экономится электроэнергия за счёт оптимальных режимов работы.
- Уходит в прошлое лишний ручной труд — больше задач решают роботы.
По исследованию компании Siemens за 2023 год, внедрение умных линий сборки сокращает расходы на обслуживание оборудования до 30%. Производство становится гибче — можно быстро менять тип выпускаемой продукции без перестройки цехов.
Суть экономии проще всего увидеть на цифрах:
Показатель | До внедрения | После внедрения |
---|---|---|
Производственные отходы | 6% | 2% |
Простои оборудования | 18 часов/месяц | 7 часов/месяц |
Число брака | 4% | 1.2% |
Энергозатраты на изделие | 100% | 77% |
Серьёзные показатели, правда? Причём такой результат недостижим без внедрения новых технологий. Подключая IoT-системы или автоматическую диагностику, можно почти в реальном времени следить за здоровьем оборудования и моментально устранять сбои.
В итоге: качествo выше, сроки короче, затраты заметно падают, а конкуренты, которые так и не решились на перемены, остаются позади.
Ошибки и страхи: почему боятся инноваций
В машиностроении бояться перемен — обычное дело. Руководители часто вспоминают, как после недавнего внедрения автоматической линии три месяца ушло на настройку, а сотрудники жаловались на непонятные инструкции. Пугает и стоимость: кажется, что новая технология принесёт только затраты, а возврат инвестиций под сомнением.
Часто основная проблема — это нехватка информации и опыта. Если никто раньше не работал с системой цифрового мониторинга, почти всегда выбирают «старый проверенный способ». Ещё добавляется страх увольнений среди персонала: если завод внедрил робота, значит, «кому-то придётся уйти» — так думает часть коллектива.
Ошибки чаще всего связаны не с самими инновациями, а с организацией процесса внедрения.
- Не проводят обучение персонала — результат: сбои и поломки из-за неправильного использования.
- Недооценивают время перехода — в итоге производство тормозит дольше, чем рассчитывали.
- Выбирают решение без анализа задач — новая система оказывается бесполезной.
По данным опроса «Эксперт РА» в 2024 году, среди предприятий, внедривших инновации:
Проблема при внедрении | % компаний |
---|---|
Страх потери рабочих мест | 41% |
Недостаточная подготовка персонала | 53% |
Перерасход бюджета | 37% |
Долгий запуск | 29% |
Стоит помнить: инновации не вводятся ради галочки, а чтобы повысить качество, сделать производство гибче и избавиться от рутинных ошибок. Главное — не бояться разбирать ошибки, вовлекать людей в изменения и шаг за шагом наращивать технологичность.
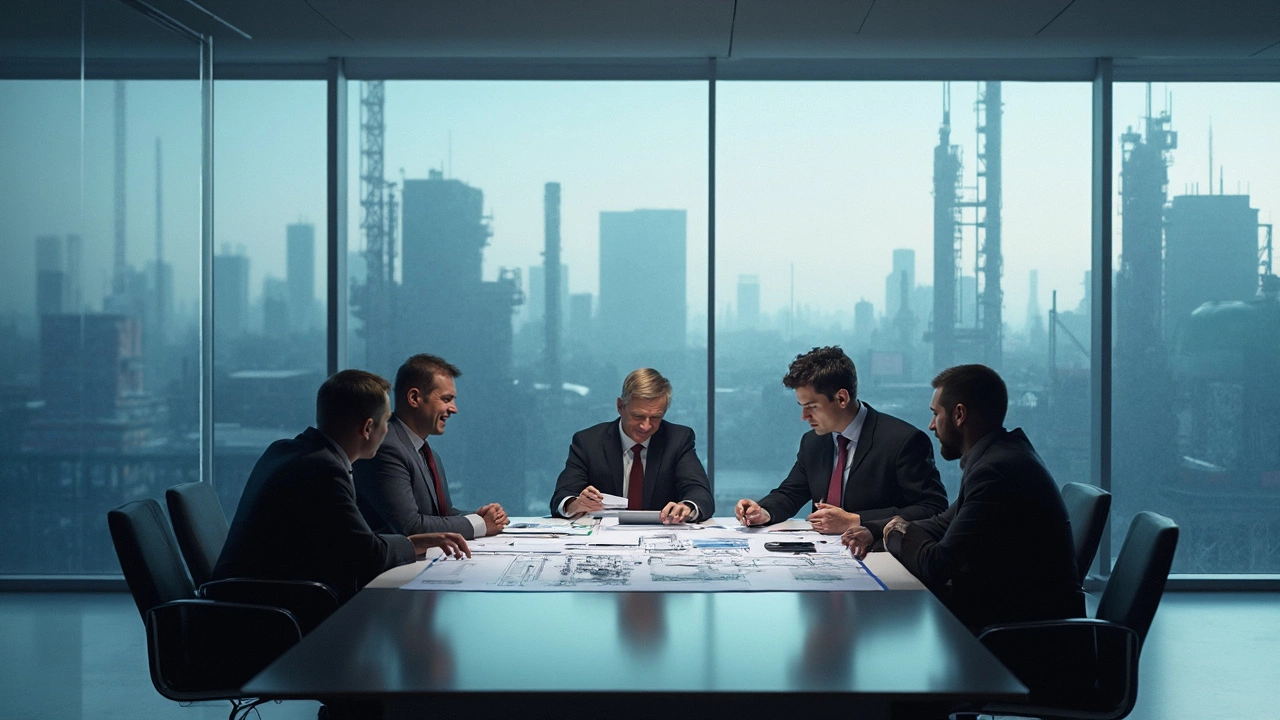
Практические советы по внедрению идей на производстве
Не каждый новаторский проект сразу становится успехом, но и ничего не делать — риск потерять позиции. Самое сложное — это начать. Вот что реально помогает производству внедрять инновации без лишней головной боли:
- Соберите идеи от сотрудников. Часто самые простые и полезные предложения приходят от тех, кто стоит у станка каждую смену. Запустите внутреннее обсуждение или анонимный сбор идей.
- Оценивайте не только «красоту» идеи, но и её окупаемость. Если внедрение позволит сократить время выполнения операции хотя бы на 5%, это уже ощутимо на больших объемах.
- Тестируйте новые решения на небольших участках. Не обязательно сразу переворачивать весь цех — достаточно выбрать одну производственную линию или отдельную операцию.
- Обучайте персонал. Даже самая крутая технология не принесет пользы, если люди не будут ее понимать. Заведите быстрые курсы или практические тренинги прямо на рабочем месте.
- Сравнивайте результаты до и после внедрения. Четкая статистика — лучший аргумент для скептиков и руководства.
В России предприятия, которые внедряли автоматизированные системы контроля за производством, сокращали число дефектов до 40% уже через год, согласно данным Ассоциации предприятий машиностроения.
Этап | Среднее время внедрения, мес. | Типичный эффект |
---|---|---|
Автоматизация сборки | 6-8 | +18% производительность |
Внедрение ERP-систем | 12-18 | -15% издержки |
Переход на цифровое проектирование | 3-6 | -22% ошибок в чертежах |
Самое важное — не затягивать процесс. На промышленных рынках стоимость промедления высокая: пока кто-то обсуждает, конкуренты уже внедряют. Даже простое обновление рабочей инструкции может ощутимо повлиять на итоговые показатели. В современном машиностроении побеждает не тот, кто дольше думает, а тот, кто быстрее пробует новое и учится на своих ошибках.
Написать комментарий