Если честно, никто не становится мировым лидером в машиностроении просто потому, что купил новое оборудование. Станки — это важно, но ключевой вопрос всегда упирается в людей. Именно кадры, их опыт и мотивация чаще всего определяют, выстрелит предприятие или скатится к выживанию. Проблем с подбором и обучением хватает у всех: от маленьких производств в глубинке до гигантов федерального уровня.
Вот встречается типичная история: инвестор поставил станки с числовым программным управлением, а работать на них некому — учили только на старых моделях. И тут никакие миллионы уже не спасают. Поэтому, если думаете, что “главный фактор” — это технологии из Японии или дешёвое сырьё, попробуйте найти инженера-технолога из поколения 25–35 лет — поймёте масштаб беды.
- Почему кадровый вопрос решает всё
- Инновации: не просто модное слово
- Поставщики и логистика: подводные камни
- Государственная поддержка и её нюансы
- Практические советы: где искать точки роста
Почему кадровый вопрос решает всё
Без хороших специалистов никакое машиностроение не работает как надо. Вот простой факт: средний возраст инженера в российских машиностроительных компаниях — уже за 45 лет. Молодых почти не видно, считается, что только "старики" могут держать уровень. Но есть нюанс: молодёжь идёт неохотно — зарплаты ниже, чем в IT-компаниях или в нефтянке, нагрузки сильные, перспективы туманные.
В 2023 году лишь 28% выпускников технических вузов выбрали работу по специальности в машиностроении. Дальше — хуже, многие через год-два меняют сферу. Такая текучка — больной вопрос даже для крупных заводов. Новички быстро выгорают, потому что сталкиваются с бюрократией, устаревшими технологиями и нулевой поддержкой.
Плюс проблема обучения. Даже если нашёл молодого сотрудника — его нужно доучить, дать реальную практику и наставника. А у предприятия не всегда есть лишние ресурсы на такую роскошь. Часто обучение идёт "по остаточному принципу": пришёл — и сразу в бой, а разбираться будешь на ходу.
В таблице видно, как обстоят дела по ключевым кадровым параметрам в машиностроении на конец 2024 года:
Показатель | Значение |
---|---|
Средний возраст персонала | 47 лет |
Доля молодых специалистов (до 35 лет) | 18% |
Текучесть кадров (за год) | 37% |
Вакансии инженеров (открытые) | более 28 000 |
Чтобы хоть как-то решать кадровую проблему, крупные компании пробуют сотрудничать с вузами: запускают стипендии, практики, дают современное оборудование для обучения. Иногда даже предлагают релокацию — оплачивают переезд специалистам из других городов. В регионах иногда работают по старинке: "передача опыта" от старших к младшим сотрудникам напрямую, но без системного подхода это малоэффективно.
Если хотите сдвинуть дело с мёртвой точки, держите пару советов:
- Не экономьте на наставниках — пусть старшие инженеры реально обучают молодёжь.
- Сделайте гибкие условия для стажёров: частичная занятость или спецпроекты для студентов.
- Внедряйте бонусы за развитие навыков: пусть за учёбу платит не только работник, но и компания.
Пока не решён кадровый вопрос — всё остальное подвисает. Технологии можно купить, а вот ценного специалиста — нет. Поэтому кадровый голод остаётся главным отраслевым фактором развития производства.
Инновации: не просто модное слово
В машиностроении инновации — не про красивые отчёты, а про выживание и рост. Тут без серьёзных перемен легко отстать на годы. В 2023 году российские заводы, которые внедряли цифровые двойники или автоматизированное проектирование, сокращали срок вывода новых изделий на рынок в среднем на 30%. Это не догадки — такая статистика есть в отчётах РСПП и профильных ассоциаций.
Люди часто думают — инновация это обязательно что-то дорогое и сложное. На практике работает простое правило: начни с автоматизации рутинных задач. Пример: обычная роботизация сварки в кузовном производстве увеличила выход годных изделий на 18% на нескольких известных предприятиях в Челябинске и Тольятти. Здесь инновация сразу даёт развитие производства и экономию на браке и переделках.
- Цифровизация процессов снижает человеческий фактор и увеличивает точность.
- Внедрение IoT помогает находить слабые места в оборудовании до того, как всё встанет.
- 3D-печать деталей экономит месяцы на логистике и закупках, особенно для ремонта уникальной техники.
И ещё один рабочий совет: не всё новое — это для гигантов. Мелкие и средние компании часто выигрывают даже от простых доработок программного обеспечения или ввода онлайн-мониторинга. Главное — не бояться тестировать. Вот честные цифры по итогам прошлого года:
Тип инновации | Эффект |
---|---|
Роботизация сборки | +22% производительность |
Внедрение ERP-системы | -17% производственные издержки |
Техническое обучение работников | +34% сокращённых аварий |
Быстрое тестирование и запуск даже простых решений — ключ к тому, чтобы развитие производства шло не только на бумаге. Каждая рабочая инновация — это шаг вперёд и экономия времени и денег.
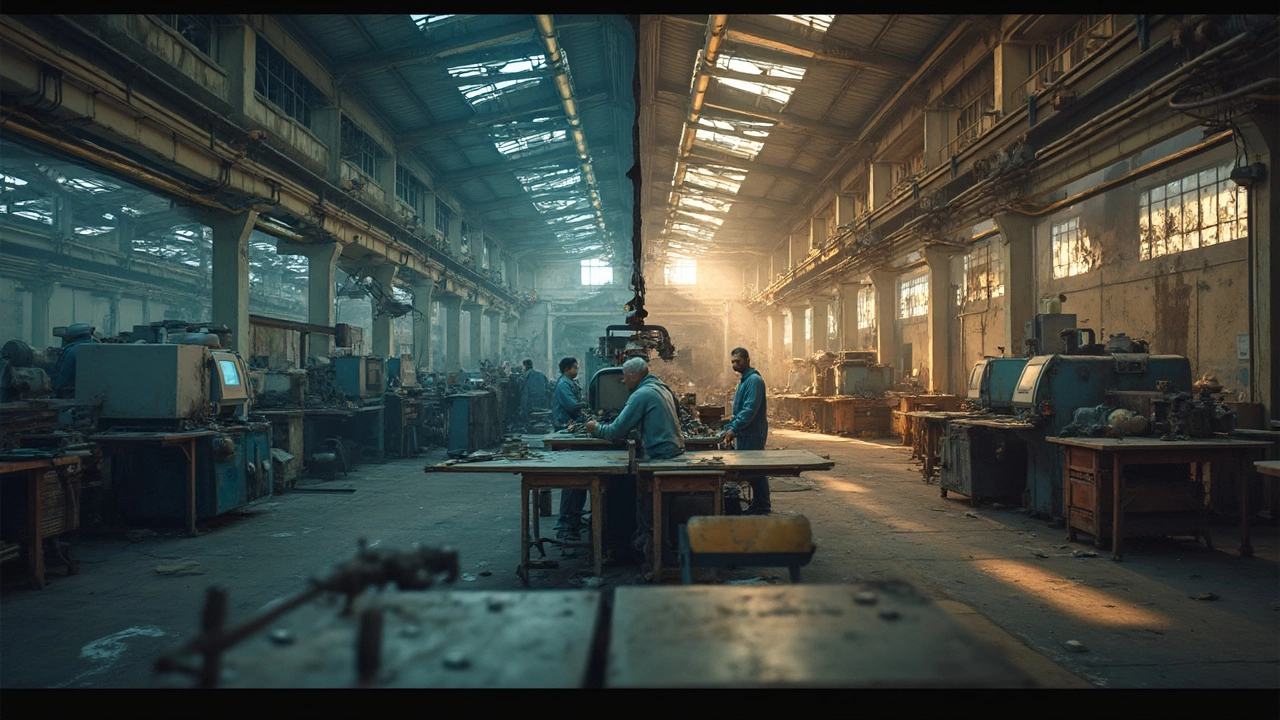
Поставщики и логистика: подводные камни
В машиностроении вопросы снабжения часто становятся ловушкой даже для сильных игроков. Каждый второй производитель хоть раз сталкивался с тем, что нужную деталь или материал ждут неделями, а то и месяцами. Почему так? Потому что слишком сложно завязаны все цепочки. Один сбой — и партия на складе мёртво стоит, простаивают люди и цеха.
Тут реально решают не только цены, но и человеческий фактор: кто, где и когда сдал поставку, как быстро отреагировали на срочный заказ, насколько понятна схема возврата брака. За последние три года задержки выросли по всей стране — поставщики всё меньше гарантируют сроки, перевозчики берут предоплату, логистика дорожает.
Недавний пример с одного из заводов в Екатеринбурге: партия подшипников из азии застряла на таможне, проект пришлось чуть ли не на полгода «заморозить». А у мелких компаний часто нет «подушки» на форс-мажоры — простаивает сборка, срывается контракт. Если брать статистику фирмы «Логистика для России», сегодня около 40% машиностроительных предприятий тратят на организацию поставок и логистики до 25% бюджета проекта.
Проблема | Распространённость |
---|---|
Сбой поставок | 70% |
Удорожание перевозки | 55% |
Долгая таможня | 40% |
Юридические сложности | 30% |
Чтобы снизить риски, компании переходят на многоканальные закупки, ищут локальных партнёров, забивают склады впрок. Вот несколько советов, которые реально работают:
- Закладывайте в план времени поставки минимум 20% «запаса».
- Ведите открытую историю проблем со снабжением — покажите руководству, где чаще всего затыки.
- Перепроверьте юр-документы с поставщиками, особенно если импортируете через третьи страны.
- Не стесняйтесь договариваться о небольших авансовых партиях, чтобы увидеть качество до основной закупки.
В итоге устойчивость к логистическим сбоям становится таким же важным фактором, как наличие оборудования или квалификации работников. Без сильных поставщиков ни одно современное производство не выйдет на нормальную мощность.
Государственная поддержка и её нюансы
Без государства продвижение в машиностроении реально идёт туго. Программы господдержки есть — только разбираться в них надо с лупой. Чаще всего это субсидии на закупку оборудования, компенсации процентов по кредитам и программы по развитию экспортного потенциала. Например, в 2024 году доля господдержки в крупных машиностроительных проектах иногда доходила до 40% затрат, если считали всё вместе: и субсидии, и налоговые льготы.
Но тут спрятан немаленький подводный камень: чтобы получить деньги, надо влезать в сложные отчёты, проходить проверки и часто тратить месяцы на бюрократию. Причём для малого и среднего бизнеса эти процедуры иногда становятся просто непреодолимым барьером. Идея здравая — а на практике выживает тот, кто нашёл хорошего бухгалтера и юриста.
- Если вы планируете подаваться на субсидию, читайте реальные кейсы коллег на отраслевых форумах. Часто там находят решения быстрее, чем в официальных документах.
- Готовьтесь к проверкам: все выплаты контролируются до копейки, особенно в рамках развития производства.
- Держите документы и бухучёт в порядке: опоздание хоть на день — и возврат денег обеспечен.
Есть момент, про который почти не говорят — региональные программы. Они часто проще и доступнее федеральных. Например, в Татарстане и Самарской области реально получить гранты на развитие локальных проектов без лишней волокиты.
Если посмотреть на цифры, то заводы, которые пользуются разными мерами господдержки «по-максимуму», вкладывают в модернизацию оборудования до 1,5 раза больше по сравнению с теми, кто работает только на свои средства. Это видно по данным Минпромторга за 2023-2024 годы:
Тип предприятия | Средние инвестиции в модернизацию, млн руб. |
---|---|
С господдержкой | 180 |
Без господдержки | 120 |
По факту, господдержка — это не волшебная палочка, а рабочий инструмент. Кто грамотно им пользуется, тот выигрывает на длинной дистанции. Но и усилий тут требуется не меньше, чем при запуске самого производства.
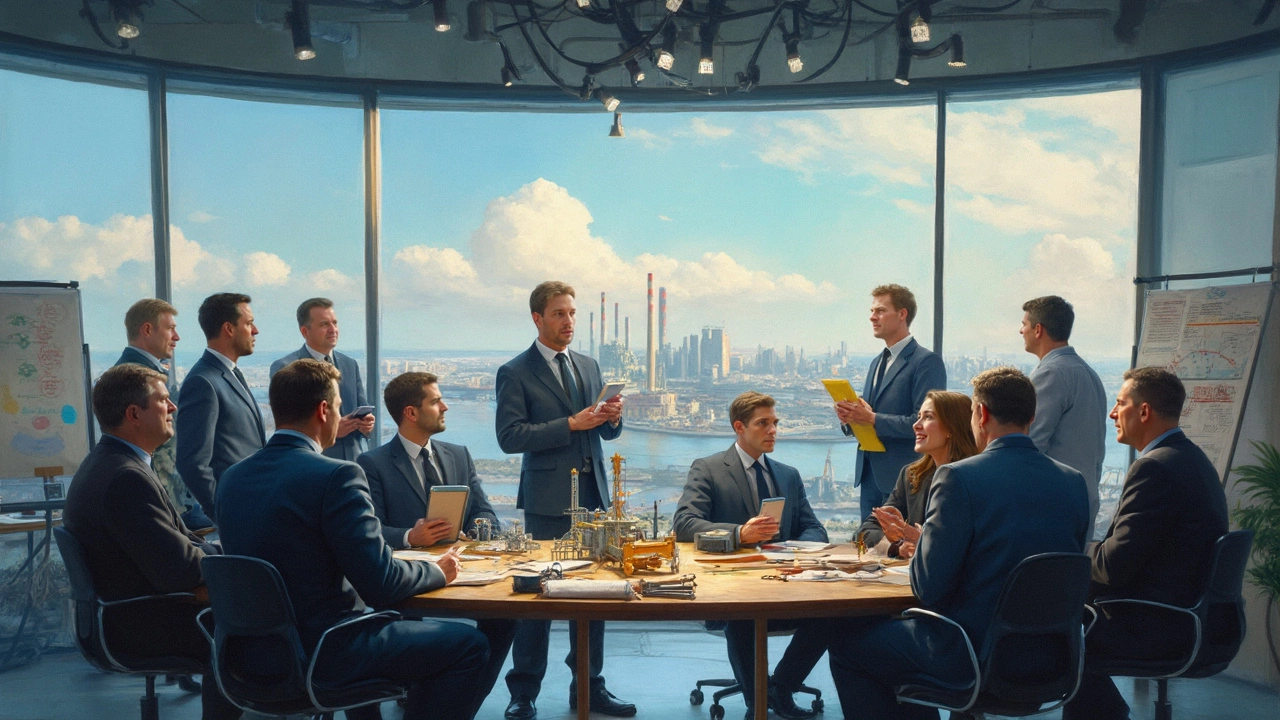
Практические советы: где искать точки роста
В машиностроении обычно ждут магических решений сверху, но реальные точки роста часто лежат под ногами — нужно только внимательно посмотреть. Вот что реально работает:
- Анализ потерь времени и ресурсов. Проверьте любые повторяющиеся действия и простои — почти всегда обнаруживаются ненужные шаги в логистике, избыточные перемещения деталей и ожидания у станков. Часто простые перестановки оборудования увеличивают производительность на 10–15% без больших вложений.
- Внедрение бережливого производства. Не нужно сразу запускать полный Lean-процесс — начните с «5С» на рабочих местах и мини-аудитов. Например, на крупных заводах после внедрения 5С затраты на внутренний транспорт сократились почти на 20%.
- Прокачка персонала. Не стоит недооценивать внешнее обучение и внутренние мини-курсы. Даже приглашённый практик из соседнего завода может показать фишки, которые месяцами экономят часы работы.
- Пересмотр цепочек поставок. Регулярно мониторьте качество и сроки поставок. Чтобы снизить простой, держите 2–3 ключевых альтернативных поставщика — это уже практика у многих ведущих предприятий отрасли.
- Внедрение цифровых инструментов. Простейший электронный учёт производства или онлайн-планировщик часто добавляет прозрачность и ускоряет реакции. Даже доступное бесплатное ПО может существенно облегчить планирование на первом этапе.
Чтобы не быть голословным, вот короткая сводка, на что обращают внимание производственные компании, когда ищут точки роста:
Фокус | Средний прирост эффективности |
---|---|
Оптимизация логистики | 10–15% |
Мотивация персонала | 5–12% |
Внедрение цифровых решений | 8–17% |
Бережливое производство (5С и др.) | 10–20% |
Самое важное — не ждать идеальных условий или распоряжений сверху. Вводить изменения, отслеживать результат и вовлекать в эти процессы всех — только так появляются реальные точки роста в машиностроении и при этом минимальные расходы.
Написать комментарий