Когда у тебя на заводе оборудование старше тебя самого, сложно понять, зачем вообще всё менять. Но цифровизация — это не про красивые слова из рекламных буклетов. Это про то, что данные больше не теряются где-то на бумажках, станки не простаивают из-за глупых ошибок, а ты видишь всё, что творится на производстве, буквально с телефона.
Такой подход позволяет быстро находить узкие места, где компания теряет деньги и время. Автоматизированные системы считают сырьё, энергию и даже работоспособность сотрудников. Не нравится, что смена простаивает по 20 минут в день? Теперь ты видишь это на графике и можешь реагировать сразу, а не через месяц, когда уже поздно что-то менять.
- Что такое цифровизация производства и как это выглядит на деле
- Как цифровые инструменты меняют повседневную работу
- Фишки, которые реально экономят время и деньги
- Подводные камни и что мешает внедрять новое
Что такое цифровизация производства и как это выглядит на деле
Цифровизация производства — это процесс, когда привычные задачи перекладывают на компьютерные системы, датчики и подключённые устройства. Например, показания температуры или давления теперь собирают не вручную, а автоматически передают на общий сервер. Всё это помогает видеть картину по каждому участку или цеху хоть в реальном времени, хоть за последний месяц.
Раньше на заводах куча данных записывалась от руки. Таблички терялись, цифры искажались случайно или специально, руководитель часто узнавал о проблемах слишком поздно. С цифровыми решениями всё поменялось:
- Все показатели оборудования и ресурсов идут прямо в электронную систему.
- Даже простые сканеры штрих-кодов значительно ускоряют инвентаризацию на складе.
- Планирование выпуска и заказов теперь идёт автоматически, без тысячи звонков и бумаг.
- Ошибка одного оператора больше не ведёт к простоям или большим потерям.
Один завод в Тольятти после внедрения цифровых датчиков сокращал простои оборудования с 18% до 6% за год. Это в среднем по отрасли 200–300 часов рабочего времени экономии, и это только один показатель.
Процесс | До цифровизации | После цифровизации |
---|---|---|
Планирование производства | До 8 часов/смена | Не более 1 часа/смена |
Потери от ошибок | ~12% выпуска | <2% выпуска |
Поиск проблемы | До 2 дней | Минуты |
Самое важное — цифровизация не означает, что роботы вытесняют людей. Владельцы компаний рассказывают: высвобождаются ресурсы на развитие, а сотрудники переучиваются на новые, более интересные задачи.
Как цифровые инструменты меняют повседневную работу
Ощущения, что цифровизация — это что-то далёкое, быстро исчезают, когда видишь, как меняется обычный рабочий день. Один из главных плюсов — исчезают бесконечные бумажки, путаница с заказами и пресловутый человеческий фактор, из-за которого чаще всего возникают ошибки.
Данные теперь не хранятся в тетрадях, а собираются в одной системе и доступны всем ответственным сразу. Бригадиров уже не надо искать — они могут онлайн проверять выполнение смены, а технолог видит точные параметры аппаратуры прямо на планшете. Инженеры получают уведомления, если где-то пошёл сбой. Нет нужды ходить по цеху и спрашивать: "Ну что там у вас?" Всё видно вживую на экране.
Реальный пример — внедрение датчиков контроля температуры и вибрации на станках. Если параметры выходят за пределы нормы, система тут же шлёт сигнал мастеру. Это помогает поймать поломку на ранней стадии и избежать больших затрат на ремонт. Рабочие получают чёткие инструкции, что делать — не надо гадать или вспоминать старые привычки.
Ещё один плюс — прозрачность логистики. Склады теперь ведутся цифрово, и очень сложно "случайно" списать лишнее сырьё. А если что-то заканчивается — система предупредит заранее. Всё это ускоряет заказы, уменьшает простои, увеличивает эффективность работы.
Вот показатели из отчёта российского предприятия по металлообработке после внедрения цифровизации за полгода:
Показатель | До | После |
---|---|---|
Кол-во простоев | 15 минут/день | 4 минуты/день |
Ошибка в заказах | 8% | 2% |
Продуктивность (деталей/смена) | 113 | 134 |
Самое главное — это экономит время и силы, оставляя людям возможность заниматься более сложными задачами, а не бороться с бумажками и нестыковками в графиках.
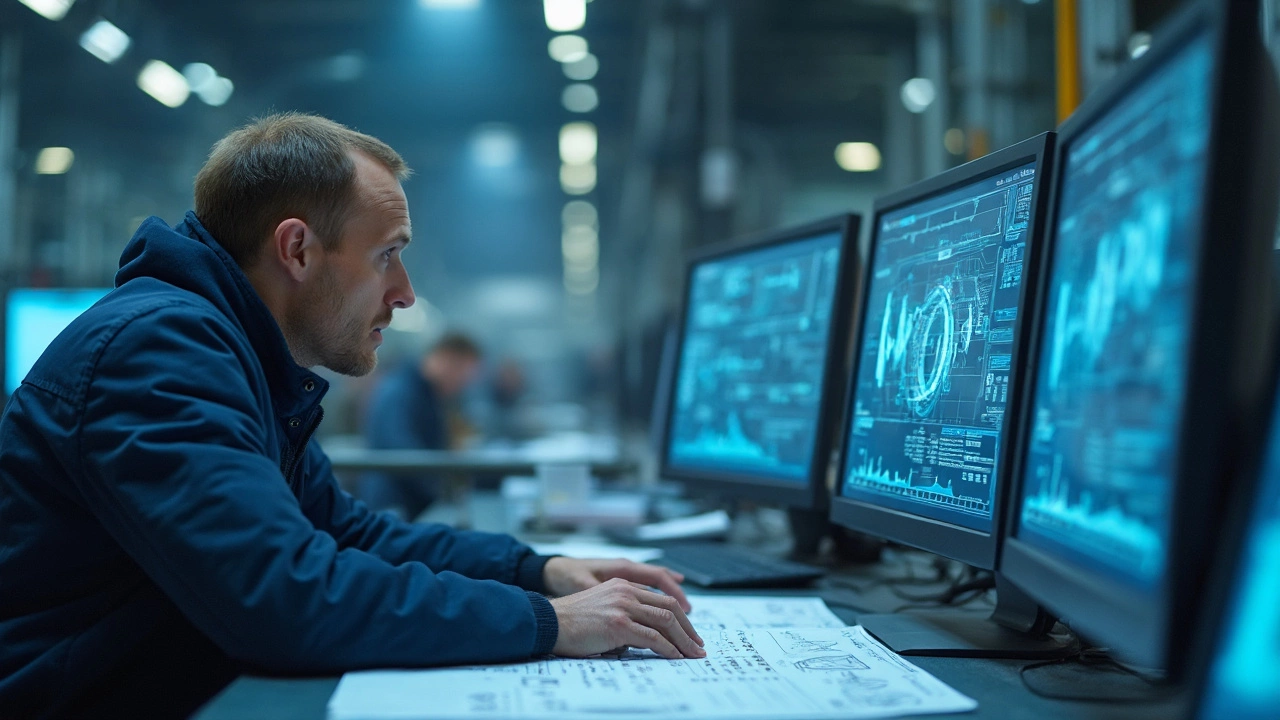
Фишки, которые реально экономят время и деньги
Самое крутое в цифровизации производства — не только скорость, но и жёсткая прозрачность во всех процессах. Например, зачем тратить три часа, чтобы узнать, сколько осталось сырья, если любой работник может посмотреть это за пару секунд прямо на мониторе? Это простая штука, но она реально экономит часы.
Один показательный кейс: на российском заводе пищевой промышленности после внедрения онлайн учета складских остатков потери сырья снизились на 14%. Это не теория — такие данные дают аналитические отчёты уже в течение первых месяцев после запуска цифровых систем.
Вот какие фишки чаще всего помогают сэкономить:
- Датчики на оборудовании собирают инфу о состоянии машин — если что-то идёт не так, техник видит это заранее и решает, до аварии дело не доходит. В результате простой уменьшается, а ремонт обходится дешевле.
- Автоматизация рутинных задач. Например, формирование отчётов, заявки на закупку, распределение смен — это всё делают роботы. Работник занимается только тем, что не может сделать машина.
- Платформы визуализации. Можно глянуть на экране состояние производства — где узкое место, а где всё идеально. Легче планировать загрузку цехов и не ошибиться с графиком работы.
- Мобильные уведомления. Если что-то внезапно ломается — уведомление у руководителя приходит на телефон. Не нужны лишние телефонные цепочки и сто кругов согласования.
Вот наглядная таблица, как меняется ситуация до и после внедрения цифровых инструментов:
Показатель | До цифровизации | После цифровизации |
---|---|---|
Средний простой оборудования | 8,5 часов/месяц | 3,2 часа/месяц |
Потери сырья | 12% | 7,5% |
Затраты времени на отчётность | 5 часов/неделя | 40 минут/неделя |
Частота аварий | 3 случая в месяц | 1 случай в месяц |
Многие заводы отмечают: когда появляется цифровизация, деньги из дыр не утекут незаметно. Всё очевидно и поправимо вовремя.
Подводные камни и что мешает внедрять новое
Многие заводы тормозят с внедрением цифровых решений, и главная причина — привычка работать «по-старинке». Люди не хотят учиться новым вещам, потому что боятся, что не справятся или просто потеряют свою работу из-за цифровизации. Уже был случай в 2023 году, когда даже простое обновление производственного софта вызвало у работников больше стресса, чем даже поломка оборудования.
Тут ещё проблема с деньгами. Новые системы стоят недёшево: закупка серверов, лицензий, обучение персонала — всё это видят не как инвестицию, а как лишние расходы. На практике, по данным отчёта Industry 4.0 за прошлый год, около 47% малых предприятий отложили обновление из-за нехватки бюджета.
Часто мешают и застарелые устройства, которые просто не дружат с цифровыми программами. Например, в списке 2024 года оказалось, что больше 30% российских предприятий работают на станках, выпущенных до 2000 года. Их «подружить» с современными сенсорами и системами можно, но это требует времени и толковых специалистов, которых на рынке не хватает.
- Сотрудники боятся изменений и не видят выгоды лично для себя
- Дорогое и старое оборудование сложно интегрировать с новыми решениями
- Не хватает специалистов, которые реально понимают цифровые процессы
- Деньги уходят на первичные внедрения, а на доработки и поддержку бюджета уже не хватает
Вот ещё реальная таблица: в 2024 году причины отказа от цифровизации выглядели так:
Причина | Процент предприятий |
---|---|
Недостаточно денег | 47% |
Старое оборудование | 32% |
Нет нужных специалистов | 21% |
Сопротивление персонала | 19% |
Получается, если начать менять производство, надо сразу думать и о людях, и о процессах, и о железе. Иначе новации просто не взлетят и будут пылиться в коробках где-то на складе, как запасные детали для несуществующих станков.
Написать комментарий